Home
artefactual evidence
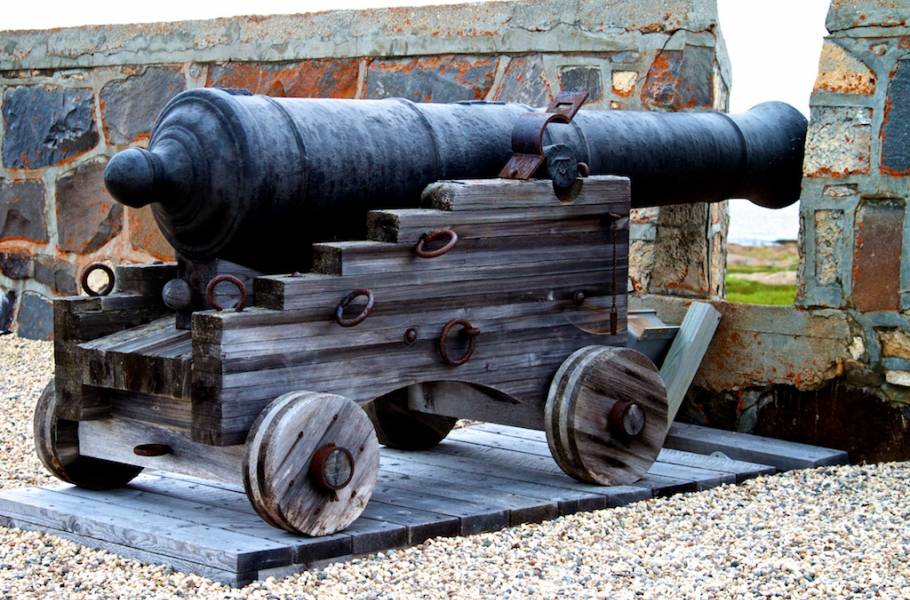
more comparative studies
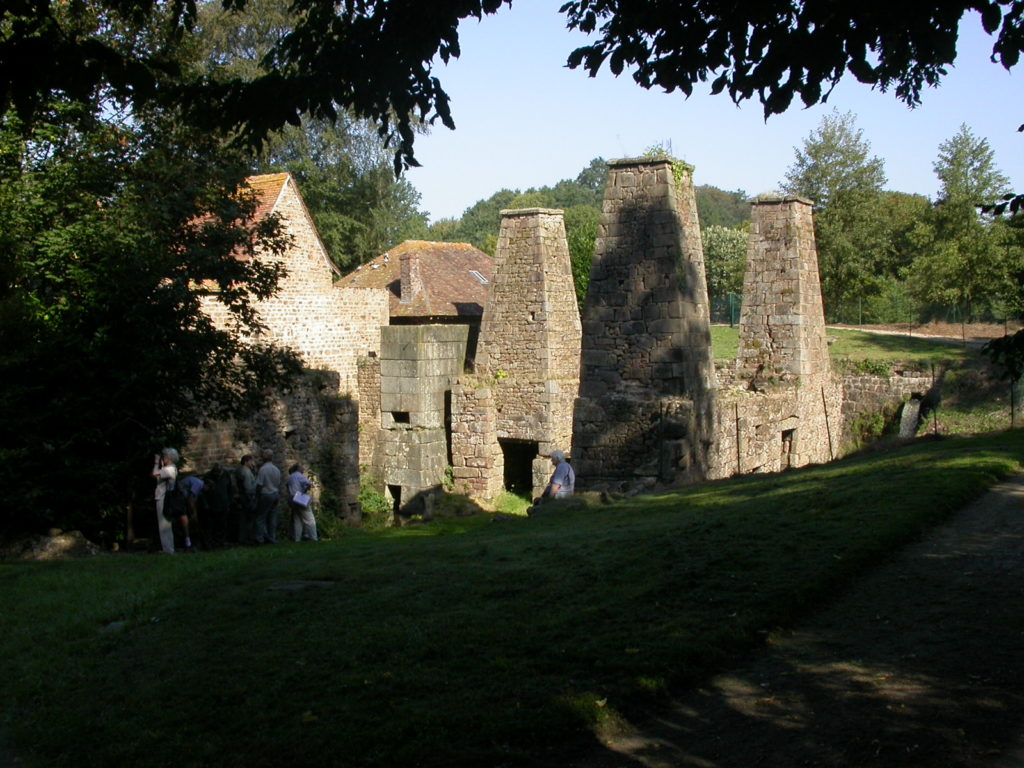
Conferences
& just digging
experimental archaeology
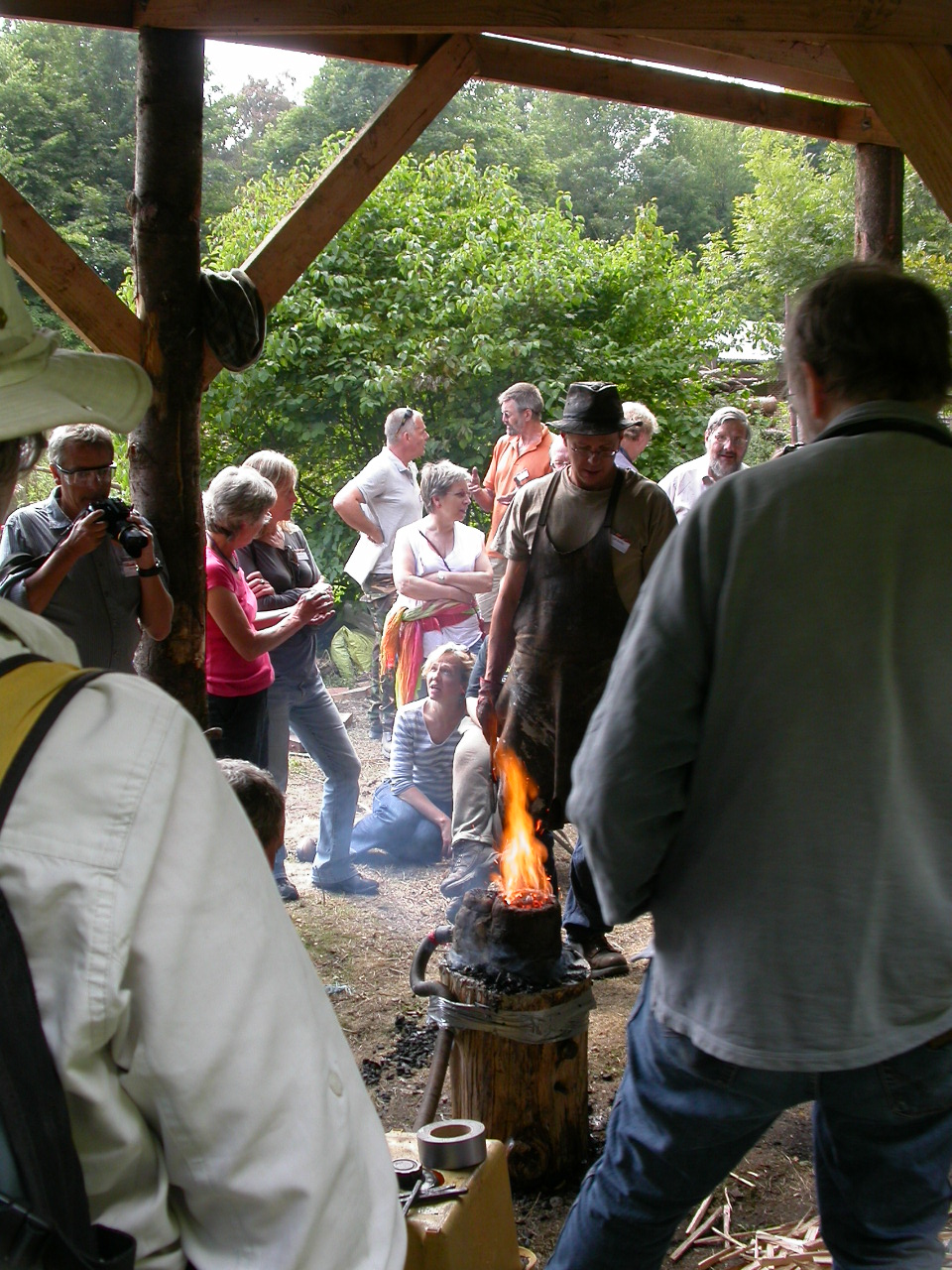
experimental reconstruction
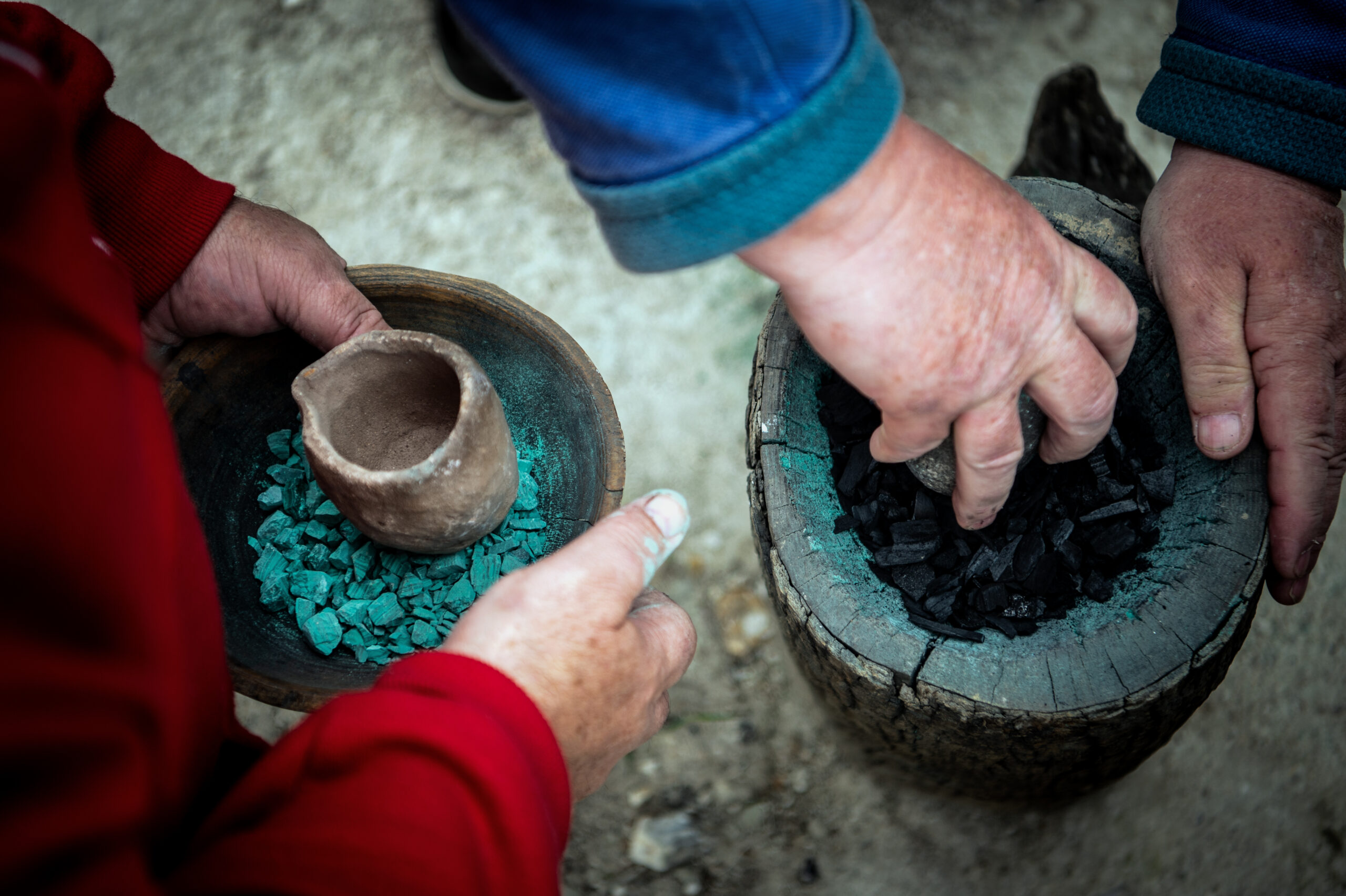
Crafts

Contents of one box in the National Slag Collection
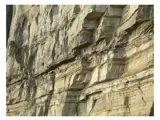
Outcrop of sideritic ore overhanging sandstone
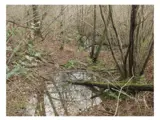
Open cast iron ore mining, Romano-British
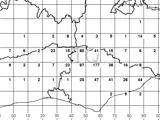
Activity frequency mapping (iron works)
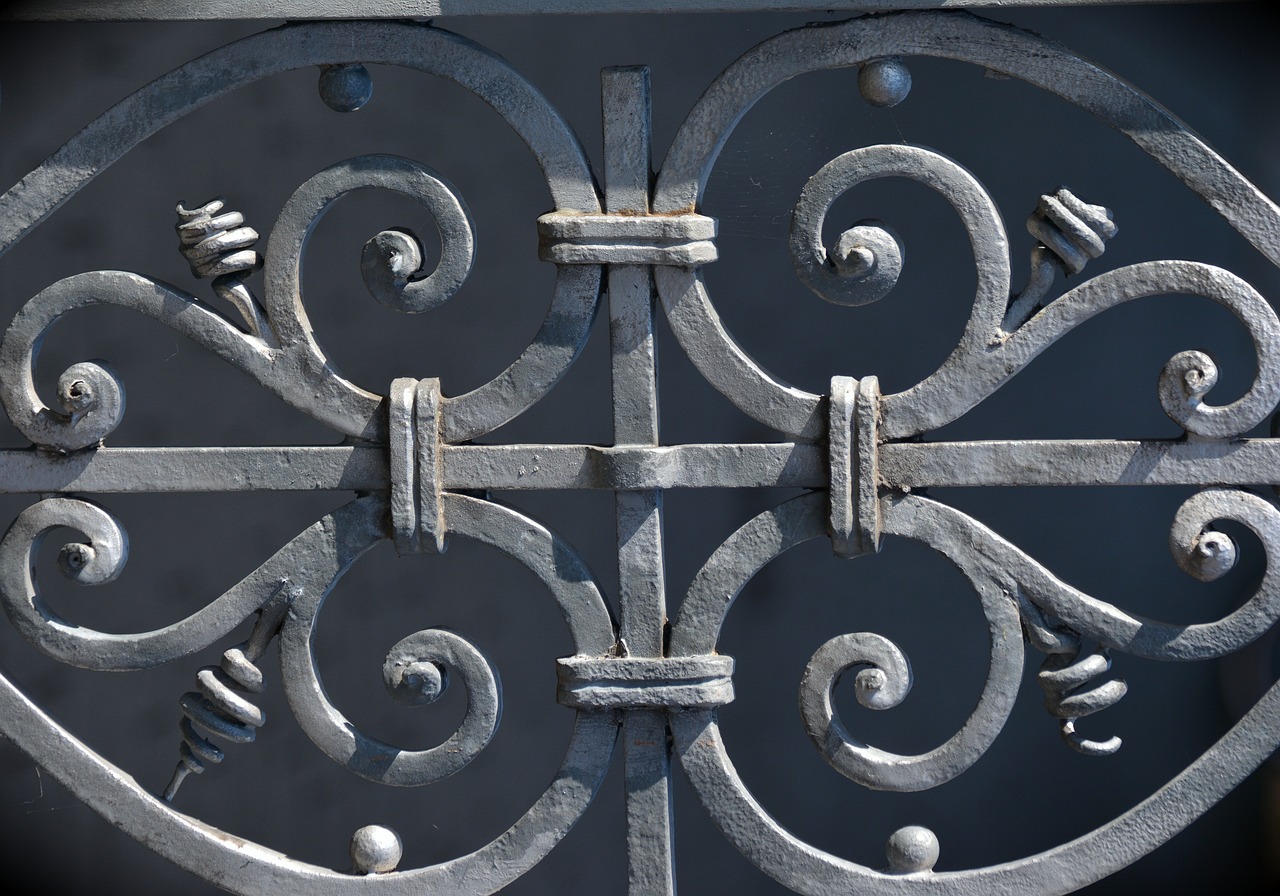
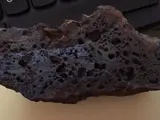
Highly vesicular bloomery slag
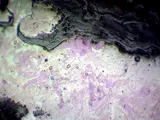
Etched sample of unworked bloomery iron (photomicrograph)
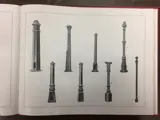
Documentary record search
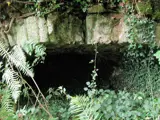
Part of an early blast furnace (Araglin, Ireland)
comparing excavated sites
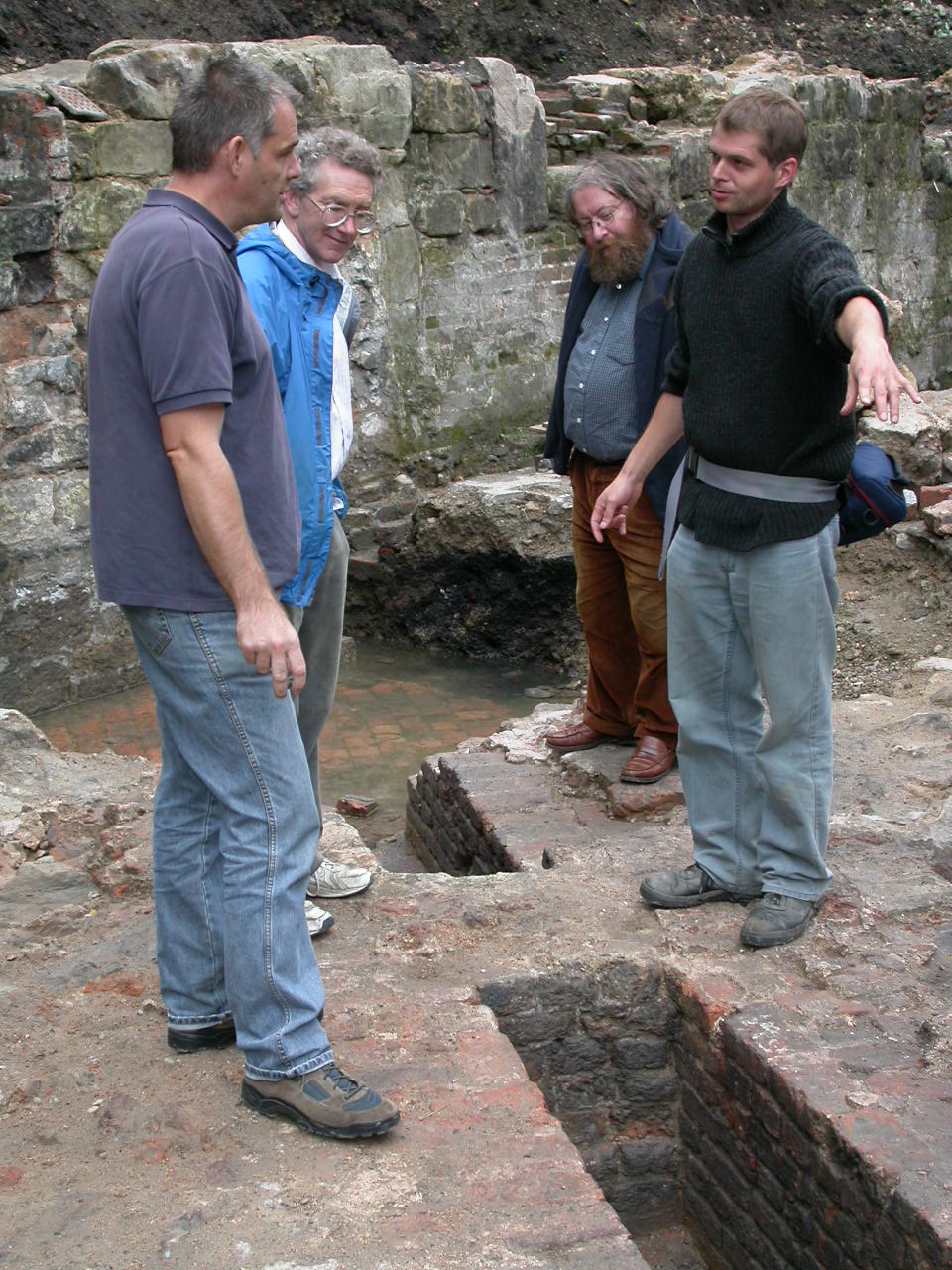