Home
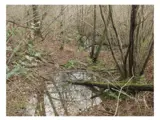
Open cast iron ore mining, Romano-British

Contents of one box in the National Slag Collection
experimental reconstruction
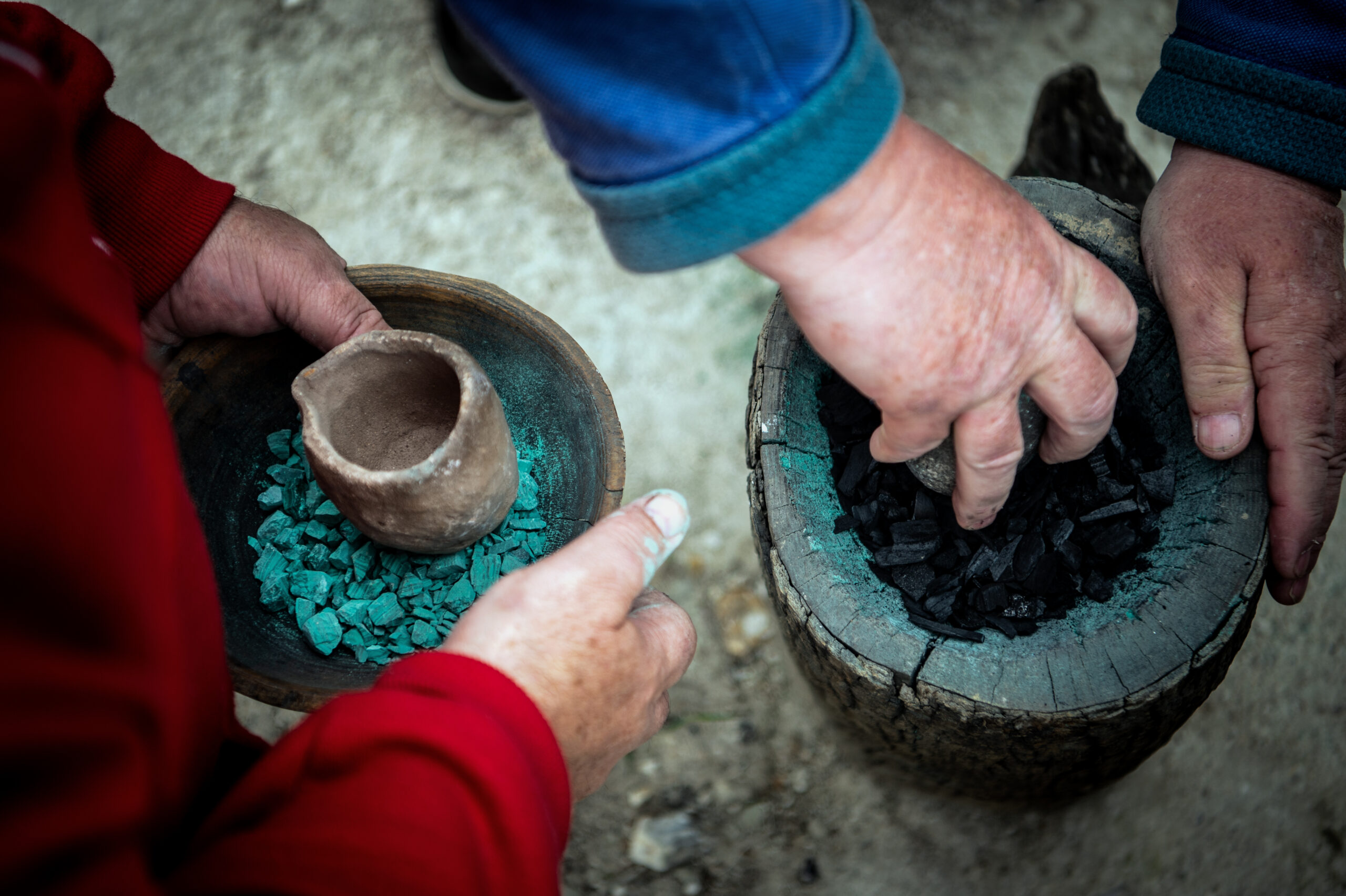
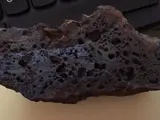
Highly vesicular bloomery slag
comparing excavated sites
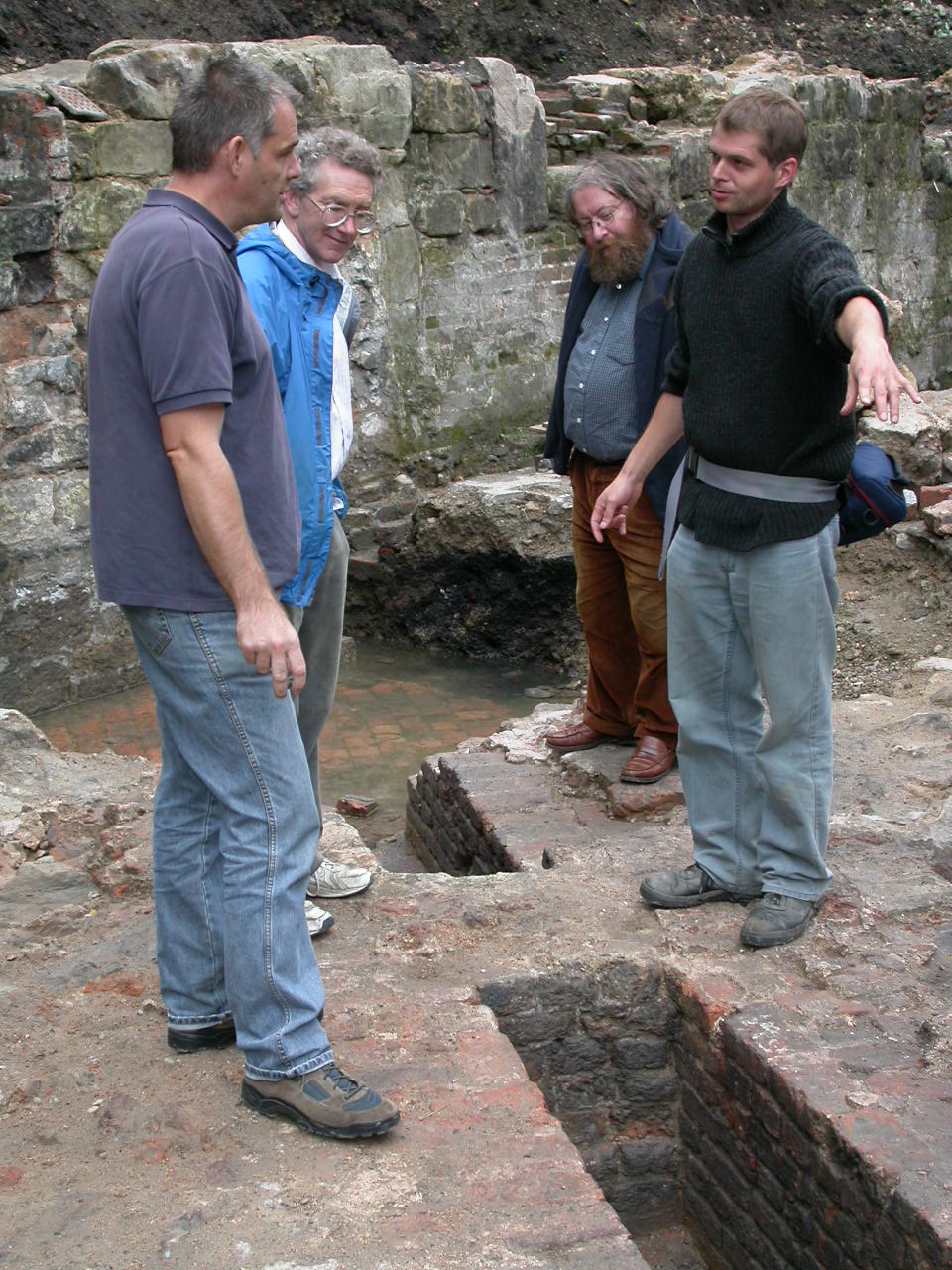
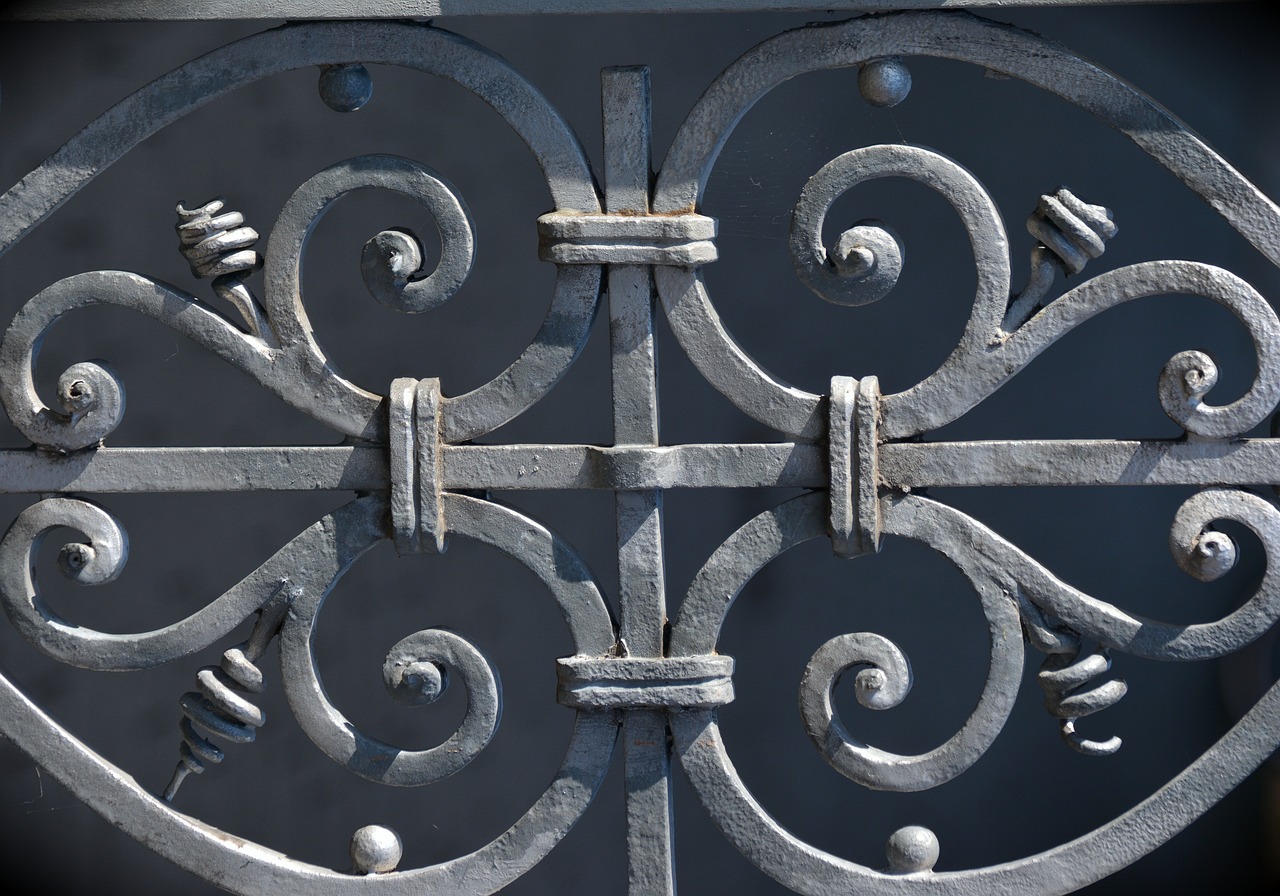
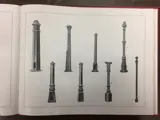
Documentary record search
more comparative studies
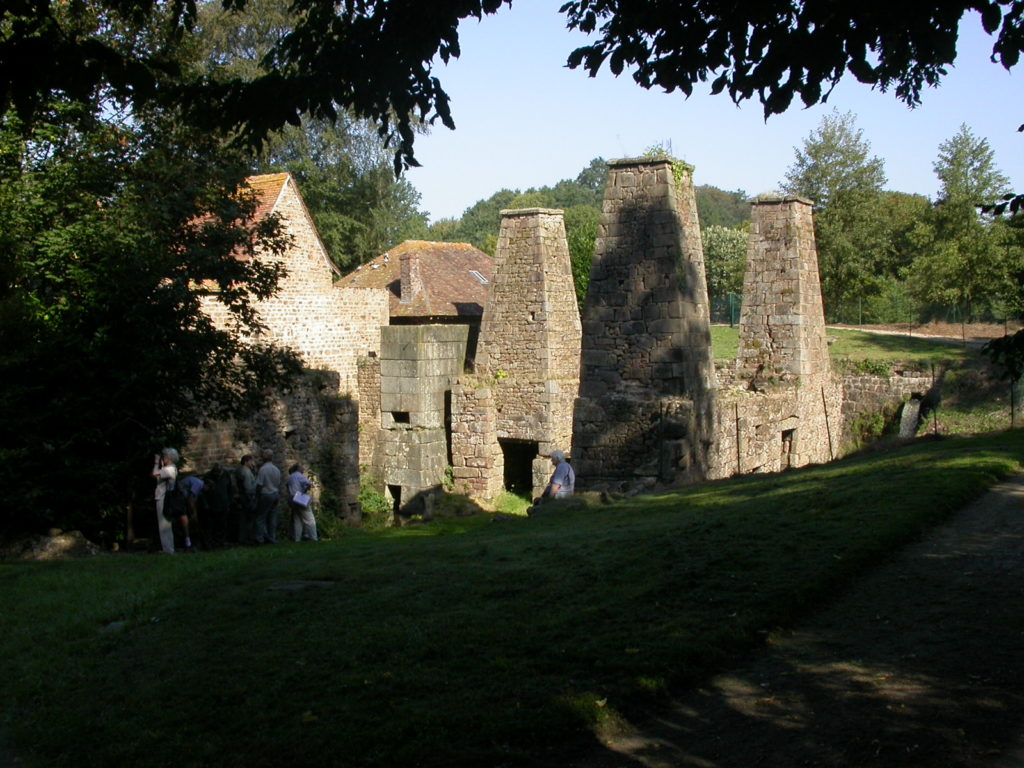
artefactual evidence
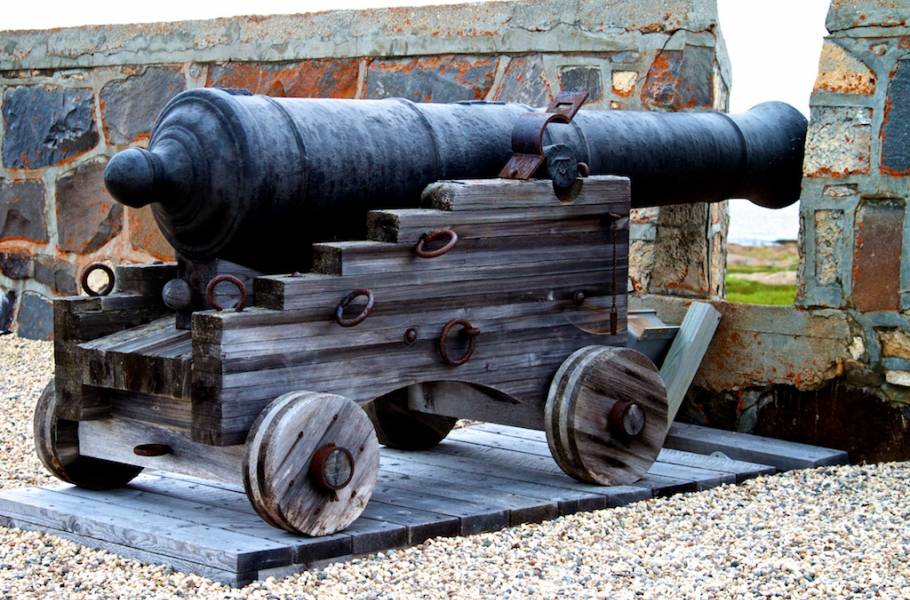
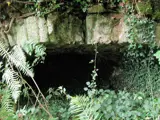
Part of an early blast furnace (Araglin, Ireland)
Conferences
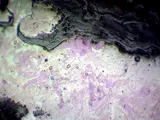
Etched sample of unworked bloomery iron (photomicrograph)
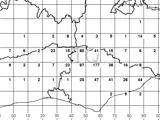
Activity frequency mapping (iron works)
& just digging
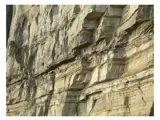
Outcrop of sideritic ore overhanging sandstone
experimental archaeology
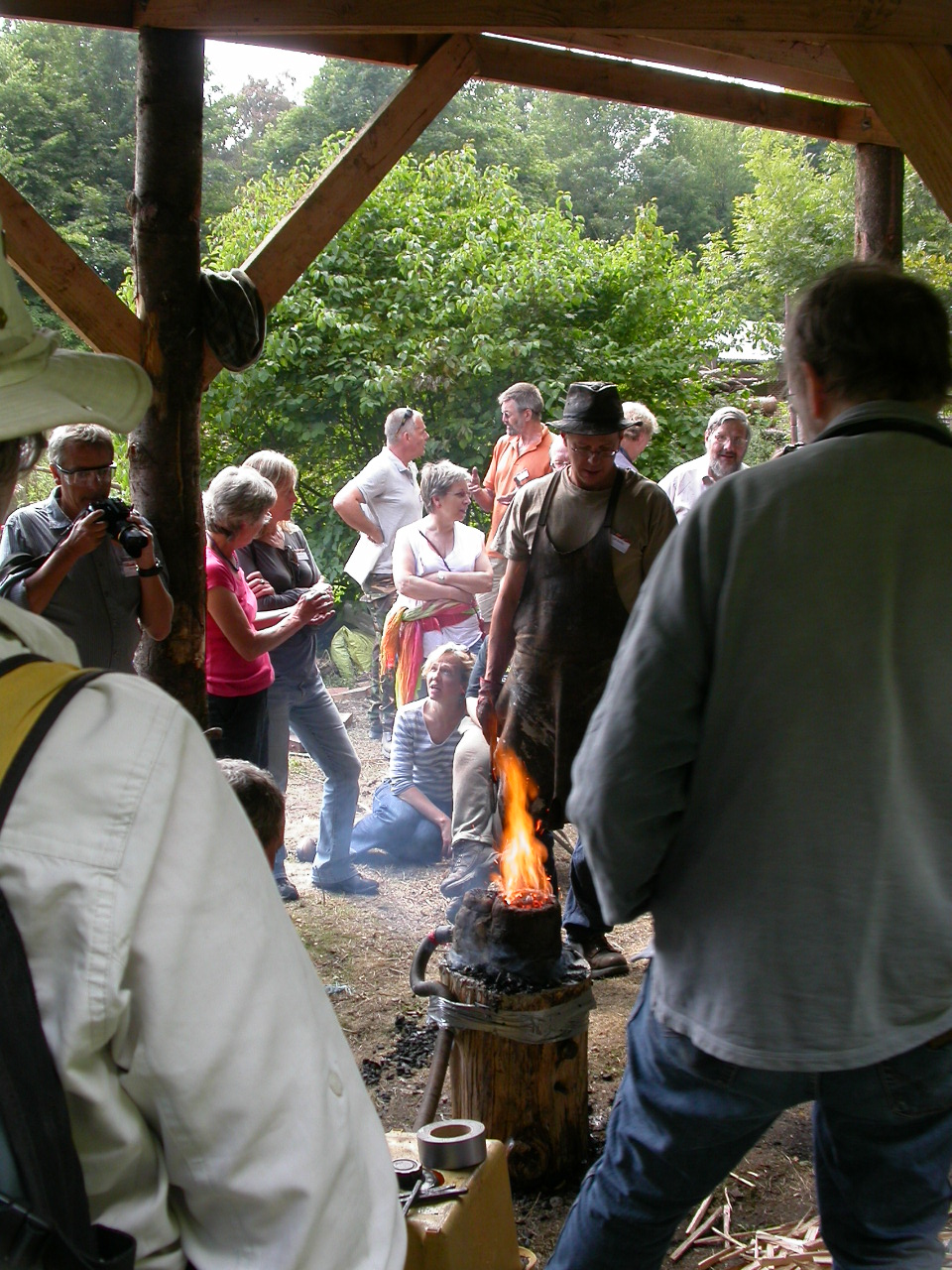
Crafts